Dako Omnis Safety Features
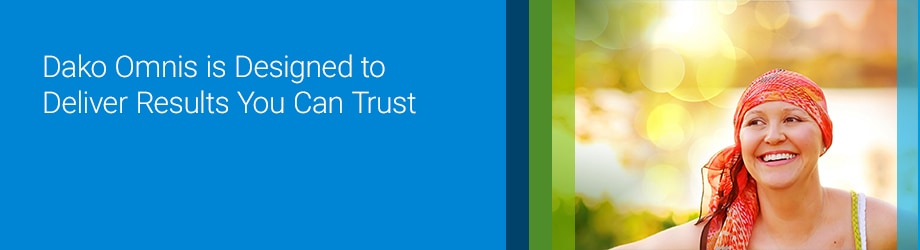

Dako Omnis is designed to provide better patient care, supporting pathology labs in delivering results they can trust, and that lead to diagnostic certainty for patients.
The fully automated IHC and ISH platform is designed with a host of integrated quality control features to reduce the risk of errors:
- By design, it is impossible to load slide racks and reagent bottles incorrectly
- To ensure optimal performance of reagents, Dako Omnis has a temperature-controlled reagent department, that keeps and monitors all 60 reagent positions continuously at 18 °C. This protects them from temperature variations due to different ongoing protocols.
- Dako Omnis includes a double check of reagents and vials to ensure that the necessary volumes are dispensed on every single slide
- In case of any discrepancies, the user will be notified, and the staining of a particular slide cannot proceed until corrected. This reduces the risk of false negatives.
Dynamic Gap staining technology was developed for Dako Omnis and supports consistent, reproducible immunohistochemical (IHC) staining.
There are many factors that may introduce variations in immunohistochemistry: the tissue itself, a range of pre-analytic and analytical factors – and the instrument performing the staining processes.
To obtain consistent, high-quality staining results it is important to optimize and standardize whenever and wherever possible.
During design of the Dako Omnis solution, there was a strong focus on preventing the staining artifacts that can happen when using other staining principles, like top-to-bottom differences, patchy staining, edge effects and air bubbles.
The glass slide with tissue is positioned at an angle of 25° to facilitate rapid reagent distribution across the slide. During reagent application, the coverlid creates a capillary gap to ensure homogeneous spreading of reagents throughout the entire staining area.
The Dynamic Gap technology addresses the factors that generate these common staining artifacts. The capillary forces that form during reagent application ensure homogeneous spread over the entire staining area, and the 25° position of the glass slides facilitate the escape of air bubbles that may be present in the reagents during application.
The goal when designing the Dynamic Gap technology was to standardize the staining environment to support consistent, uniform and high-quality staining results. Our results in international QC schemes tell us that we have reached our goal.