Access Agilent eNewsletter October 2015
>> Update My Profile | Subscribe to Access Agilent | Article Directory
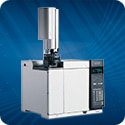
Improve your lab data, minimize downtime and costly repairs by implementing an obsolete equipment replacement plan
By Wayne Collins
Agilent Global Industry Manager
As a lab manager, what is your greatest concern? Overwhelmingly, managers tend to fear catastrophic failure of the instrument – it’s running fine one moment and then suddenly it crashes. Are you still able to provide the timely and accurate data your customers demand?
There are many consequences of a sudden instrument failure:
- The need to switch to backup instrumentation
- Loss of dedicated staff time
- Interference with scheduling of tests and disruption of normal operations
- Limited back-up capability for critical tests
- Repairs may be extensive, take too long or not even possible
- Unavailability of new replacement parts – repairs could be made with manufacturer-discontinued parts older than your instrument
- Time consuming replacement of a dead instrument could take 6 to 18 months to complete the capital process, take delivery, and set up for analysis
- Lack of timely lab data that causes a process to go out of specification – very costly in a manufacturing environment
- Dissatisfied customers may take their business elsewhere
While this scenario is bleak, catastrophic failure of the instrument may not be the worst that can happen in your lab.
Protect your busy lab’s reputation by ensuring measurement precision
Slow failure can be even more damaging because poor quality data is released to customers, often without anyone realizing it. As instrument performance degrades over time, the lab might not be aware of a problem until it’s picked up by QC procedures or customer complaints.
In a manufacturing plant, lab measurement error is usually a contributor to the variability of the process that must be controlled within product specification limits; the ability of a process to produce output within specification limits is expressed by a statistical measure known as the capability index (Cpk). The index is an indication of the ability to maintain product quality within specification limits. As measurement precision degrades, the lab contributes more to process variability, and so product quality can suffer. Off-spec products can cost thousands of dollars per hour. The lack of precision in an obsolete instrument means that the lab contributes a much greater amount of the process variability.
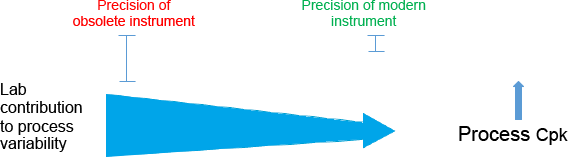
Figure 1. Illustration depicts how the use of modern precision instruments can improve lab data, helping the plant to reduce product variability and generate more money.
In a commercial lab, customers might notice poor quality results first, since they typically have more history and information about the samples. The end result of declining instrument performance is reputational damage to the lab – a credibility gap that can be expensive to redress and difficult to recover.
Declining instrument performance can seriously impact your lab’s viability
All good things must come to an end, but are you confident that your instruments will last at least until the next capital cycle? How long can you operate without them, and how much risk are you willing to take in the meantime? There are many consequences of relying on older instruments with declining performance:
- Risk of business disruption
- Poor measurement quality
- Lost productivity
- Safety/environmental incident
- Higher operating costs
- Customer operating losses
- Lab customer dissatisfaction
- Workflow hostage to software
While it is natural to focus on the financial impact of replacing an instrument, the resulting competitive advantages of updating obsolete technology might easily be overlooked, as Table 1 reveals.
Benefits |
New Instrument |
---|---|
Faster analysis |
✓ |
Lower running costs |
✓ |
Increased capacity |
✓ |
Labor savings |
✓ |
Lower consumables costs |
✓ |
Operational efficiencies |
✓ |
Higher precision |
✓ |
Greater ease-of-use; newer models are designed to be intuitive |
✓ |
Enhanced reliability |
✓ |
Option for more accessories |
✓ |
Lower maintenance requirements |
✓ |
Improved safety |
✓ |
Reduced environmental impact |
✓ |
Enhanced laboratory image |
✓ |
Enhanced staff morale with new instrumentation |
✓ |
Improved service to customers, internal and external |
✓ |
Improved regulatory compliance |
✓ |
Table 1. Benefits of updating instruments.
Planning to avoid obsolescence
What is the best way to manage obsolescence? Make a three-year capital plan where a portion, usually 20 to 30%, is set aside for replacement purposes. Then critically evaluate your instruments and schedule replacement based on the degree of obsolescence, severity of need, and the business value of new instruments. Maintain the rolling three-year plan by updating it each year.
Agilent has the tools to help you establish and maintain an effective capital plan that will keep your lab operating at full capacity, including capital planning worksheets, obsolescence evaluators, and technology business benefits.
Solve tough technical issues and improve outcomes with Agilent
Your busy lab faces complex challenges that require the support of a true business partner – one that provides key insights, helps solve tough technical problems, and dramatically improves measurable outcomes. Agilent provides a complete portfolio of instrument lifecycle service and support programs focused on your organization’s scientific and business goals.
Be confident in your obsolescence planning decisions by choosing Agilent CrossLab Service plans for your Agilent instrument and experience the benefits of our Value Promise of at least 10-years of value on your investment. With an Agilent CrossLab Service Plan, you can count on guaranteed repair or replacement of your covered instrument. For the other instruments in your technology portfolio, Agilent provides multi-vendor service support from our global network of expert service professionals – keeping downtime to a minimum. Contact your Agilent Representative today to explore how Agilent CrossLab Services can optimize your lab’s operations.
>> Update My Profile | Subscribe to Access Agilent | Article Directory