Access Agilent eNewsletter April 2015
>> Update My Profile | Subscribe to Access Agilent | Article Directory
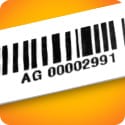
Cost-effective inventory services for busy labs with Agilent RFID
By Scott Thull
Agilent Service and Support Division
In today’s competitive environment, many laboratories are now outsourcing their inventory control functions. Because inventory management is not their core business, busy labs find themselves unable to dedicate sufficient personnel or invest in the process and tool development required to efficiently maintain an accurate inventory of laboratory assets. To address this growing need, Agilent now provides accurate, cost-effective inventory services for common lab assets – by leveraging the latest RFID technology.
Accurate asset inventories are a fundamental requirement of a successful Laboratory Asset Management Program (LAMP). Flawless execution of a well-designed LAMP improves scientific outcomes for scientists – a key element in the success of their business. Additionally, an effective LAMP process provides lab managers with service models and operational metrics that align an asset’s technical capability, capacity, and utilization with research organization protocols, SOPs and laboratory testing cycles. Deployment of a comprehensive LAMP program can potentially drive more than 20% actual cost savings from the laboratory equipment install-base and the capital asset supply chain.
Agilent’s RFID Inventory Management Service provides lab and supply chain managers with accurate, timely inventory information with minimal impact on their staff and operations. In this article, our experts describe the foundation of a successful LAMP program and provide tips for implementation.
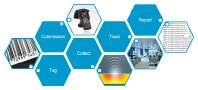
Figure 1. Agilent RFID Inventory Management Service process.
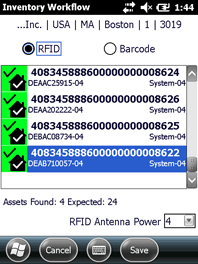
Figure 2. An example of individual assets identified as a single ‘System’.
Tips for accuracy and precision that reduce risk
From recent interviews, Agilent discovered that inventory records kept by customers are often found to be less than 80% accurate. This equates to tracking hundreds or thousands of assets that are either missing or have incorrect descriptions, locations or other attributes. However, by using specially developed software and processes, Agilent’s RFID Inventory Management Service can provide labs with 95% or better inventory accuracy (Figure 1).
Sophisticated laboratory instruments often consist of several interconnected modules. The Agilent RFID Inventory Management Service understands the importance of the relationship between these modules and integrates them into a ‘System’ (Figure 2). This process helps assure that inventory is not only accurate at the module level, but also has sufficient precision to model the system level at which the instrument operates.
Poor inventory accuracy introduces both financial and operational risk into your operations. Some examples of risk to consider include:
- Instrument modules in cGxP laboratories may be exchanged and the resulting instrument configuration is no longer compliant.
- Redundant instrument purchases may occur due to lack of visibility to existing assets.
- Staff resources are unnecessarily deployed to locate missing assets that in fact were incorrectly identified or simply overlooked during the inventory.
- Financial metrics such as depreciation are understated due to missing assets or the failure to account for instruments purchased or disposed of during a business cycle.
Resource requirements reduced
Asset management and inventory operations are routinely performed by existing laboratory or maintenance staff. As lab resources are typically assigned to other responsibilities of higher priority, inventory operations can often incur added expenses from overtime and weekend assignments. Agilent RFID Inventory Management Services leverage your existing staff and other specially trained resources – assuring inventory quality is consistent from site-to-site and year-to-year.

Figure 3. Agilent RFID tags are sized to fit a variety of common laboratory assets.
Agilent’s RFID based inventory service can identify several assets at once, including those that may be inside of a hood or stored in a cabinet. Combined with a variety of RFID tag options (Figure 3), the efficiency of this service allows Agilent to perform future inventory operations during normal laboratory hours with minimal impact on your ongoing operation.
Time savings realized
Labs that utilize conventional inventory methods, along with internal resources, often require several weeks or even months to complete their inventory. The duration of time required to finalize each inventory prohibits more frequent inventory validations – even though timely, updated inventory validations would be beneficial to the bottom-line. After application of RFID tags to existing assets, the Agilent RFID Inventory Management Service can complete most inventory operations in less than one week – and at most sites in less than one day.
Global solution for improved productivity
Agilent RFID Inventory Management Services have already been installed and site-tested by several forward looking labs and will be available for order worldwide beginning Spring 2015. Contact your Agilent Authorized Distributor or Agilent Sales Representative today to learn how Agilent can help you achieve a more accurate and timely inventory information system. Then watch a short video to better understand how Agilent CrossLab Enterprise Services could benefit your lab.
>> Update My Profile | Subscribe to Access Agilent | Article Directory