Access Agilent eNewsletter October 2015
>> Update My Profile | Subscribe to Access Agilent | Article Directory
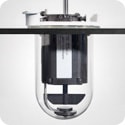
Use early warning signs to keep your dissolution laboratory running smoothly
By Bryan Crist
Agilent Dissolution Systems – Scientific Affairs Manager
Has this happened in your busy lab? A routine dissolution apparatus qualification results in an out-of-tolerance measurement and the cause is confirmed to be a mechanical issue that affected apparatus alignment. In 21 CFR Part 211.160(b)(4), GMP states “…Instruments, apparatus, gauges and recording devices not meeting established specifications shall not be used.” This means downtime for the apparatus, which presents several problems. The apparatus would require service or mechanical adjustment, followed by a full enhanced Mechanical Qualification (eMQ) to measure and document that the apparatus again conforms to specification. In due diligence, a comprehensive review is conducted of the dissolution test and results from all drug products tested and released since the last time that the apparatus was found in conformance. These retrospective reviews and possible retests often require significant time and expense to perform, which can be damaging to a laboratory’s reputation and productivity.
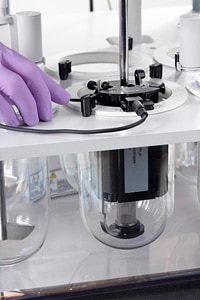
Figure 1. Agilent’s 280-DS MQS makes physical parameter monitoring quick and easy.
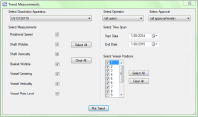
Figure 2. Trending filters of the 280-DS MQS software provide a way to detect problems before they happen.
Quick, easy, accurate trending with Agilent 280-DS solution
The Agilent 280-DS Mechanical Qualification System (MQS) has been developed exclusively to measure and report all physical parameters required by the FDA and ASTM standards for enhanced mechanical qualification of USP Apparatus 1 and 2. The instrument has two components – vessel module and instrument module – which are capable of taking each of the physical parameter measurements at each active vessel location for paddles or baskets in about 15 minutes (Figure 1). The high-precision construction of the device allows it to take accurate measurements at the exact positions required by the MQ standards. Reproducibility is enhanced by elimination of data interpretation and the hands-free design of the modules. The reporting of results documents that the apparatus is within the rigorous tolerances found in the eMQ standards.
In addition to all of the features of the Agilent 280-DS MQS, an added benefit is realized through the ability of Agilent 280-DS MQS Workstation Software to store all data for trend analysis on any 280-DS compatible dissolution apparatus in your laboratory. Imagine if you could remove an apparatus from service before it actually fails. For instance, a centering measurement in the lower portion of the vessel increases slowly over time from 0.1 mm, to 0.3 mm, to 0.6 mm, and then 0.9 mm. Using the data collected by the 280-DS software, you would have the ability to take the apparatus off line for service prior to reaching a failing calibration result. This capability not only meets but exceeds regulatory expectations to maintain apparatus between calibration intervals and its value is realized in laboratory operating costs and time (Figure 2).
Minimize investigations with increased frequency of qualifications
Another critical step in minimizing the occurrence of calibration failure is to establish the frequency of requalification based on risk assessment of components or parameters that are more susceptible to falling out of tolerance. In the FDA-enhanced MQ procedure, frequency has been communicated as: upon receipt, after the instrument is moved or repaired, and six months after the previous calibration. [1] Although this recommendation covers the minimum frequency for the full MQ battery of tests, the FDA Guidance for Industry further suggests that the GMP laboratory “calibration procedure should specify the frequency at which each calibration step is to be performed. Calibration schedules should take into account the potential for variation in each parameter known to be critical.” [2] This suggests that some parameters, which could fall out of tolerance more easily, should be measured more often – perhaps quarterly, monthly, or as needed – to verify that the component remains within mechanical tolerance.
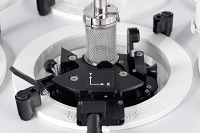
Figure 3. A more frequent periodic qualification interval increases visibility and lessens the chance of failure investigations.
The frequency of performing intermittent checks such as height and centering after exchanging paddle and basket shafts, for instance, should be evaluated based on the instrument design and clearly stated in the SOP covering dissolution apparatus qualification (Figure 3). Detrimental FDA observations for dissolution apparatus qualification most often come from not having written SOPs that outline the procedures and frequencies for MQ, having insufficient procedures, or simply not following the SOPs. It is imperative that the laboratory has well-established SOPs on apparatus requalification in which analysts have been thoroughly trained.
Increase uptime and precision using Agilent 280-DS MQS in your lab
Agilent provides a comprehensive solution for maintaining dissolution apparatus in top condition and alignment as required by GMP to ensure high-quality pharmaceutical products. For additional information, visit our Online Source Book for Agilent 280-DS MQS information as well as links to implementation guidance and regulatory information about eMQ, or download an informative brochure about the Agilent 280-DS Mechanical Qualification System.
- Mechanical Qualification of Dissolution Apparatus 1 and 2, FDA Division of Pharmaceutical Analysis, Document DPA-LOP.002, June 2, 2006.
- The Use of Mechanical Calibration of Dissolution Apparatus 1 and 2 – CGMP, US FDA Center for Drug Evaluation and Research (CDER), January, 2010.
>> Update My Profile | Subscribe to Access Agilent | Article Directory