Access Agilent eNewsletter April 2015
>> Update My Profile | Subscribe to Access Agilent | Article Directory
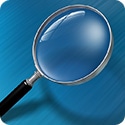
Reduce measurement time and minimize dissolution apparatus failures with the Agilent Mechanical Qualification System
By Dan Spisak and Bryan Crist
Agilent Dissolution Systems
Dissolution apparatus is comprised of a sample preparation system that relies on numerous precisely maintained physical parameters to produce consistent and reliable results. Samples are periodically withdrawn during testing and analyzed by UV or HPLC methods to ensure established drug release specifications are met.
The need for regularly qualified dissolution apparatus is key to maintaining and protecting a pharmaceutical manufacturer’s reputation. Failures, as well as any related investigations, can be costly, time consuming, and cause serious compliance issues.
To maintain peak performance, dissolution apparatus is periodically qualified to verify it is operating within established enhanced mechanical specifications and tolerances. When qualification results are not within the specifications, a laboratory investigation is required to determine the root cause of the problem, as well as any required adjustments and requalification of equipment. Additionally, a second investigation is needed to determine the impact of the failure on live samples that have been tested and released on the apparatus.
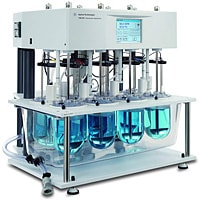
Figure 1. Control of the dissolution apparatus’ physical parameters is critical for consistent and repeatable results.
Good Manufacturing Practices (GMP) compliance requires a valid, documented reason for calibration failures or out-of-specification (OOS) results. It is not an option to simply re-run the dissolution experiment or make an adjustment. A detailed examination of the OOS must demonstrate the extent that the issue had on the integrity of results since the last time the apparatus was measured and found within tolerance. The apparatus manufacturer has a responsibility to design and manufacture the dissolution apparatus according to the specifications listed in the harmonized United States Pharmacopeia (USP) or equivalent enhanced mechanical qualification procedures. Ideally, instrument quality and proper care by the users should limit variation of results regardless of the dosage form being tested. Periodic qualification of the apparatus verifies that these standards are met on a continuous basis– typically occurring every six months using the USP Performance Verification Test (PVT) or enhanced Mechanical Qualification (MQ) as prescribed by the US Food and Drug Administration (FDA) or American Society for Testing and Materials International (ASTM).
Tip: There are several interesting ways to reduce the number of failures
First, decrease the amount of time between scheduled qualifications. Second, analyze the data more vigorously. For example, qualifying all instrumentation every three months (rather than a traditional 6-month interval) would cut the amount of suspect data in half. Third, combining this more frequent testing schedule with a more proactive approach to spotting patterns in data approaching out-of-tolerance values would help to minimize or even eliminate instrument-related failures.
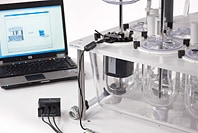
Figure 2. The Agilent 280-DS MQS eliminates all uncertainty, interpretation and variability with hands-free measurements.
Agilent 280-DS Mechanical Qualification System and MQ implementation
Physical parameter verification of the dissolution apparatus has always been required before dissolution tests and periodically as part of Performance Qualification (PQ) testing. One key advantage of enhanced Mechanical Qualification (MQ) implementation is efficient time management. Users can perform MQ measurements with considerably less downtime, allowing tests to be run more often, while streamlining scheduling. These timesavings can be significant. Greater efficiency and reduced instrument downtime can also be achieved by including periodic testing – daily, weekly, monthly, or quarterly – into the routine care and maintenance schedule of dissolution equipment. This approach will help to prevent future system failures and related downtime. With the ability to reduce measurement time in combination with its software trending feature, Agilent’s 280-DS MQS can identify problems before a parameter is out of specification. For instance, steadily increasing paddle wobble measurements from month to month could be detected and corrected before becoming an OOS value. The MQ procedure allows for a robust evaluation schedule to exist with a very manageable time commitment. When coupled with the Agilent 280-DS MQS and its software data trending capability, problems can be proactively addressed and failure investigations improved dramatically. For additional tips, feel free to download the MQ issue of Practical Solutions, chat with your peers on the Dissolution Discussion Group (DDG), or ask our in-house experts via the Dissolution Hotline.
Agilent offers a vast array of dissolution products, services, and support
Agilent offers a portfolio of dissolution products that meet all USP, EP and JP guidelines and integrate the latest technological advances backed by comprehensive service, support, and training. You can view these dissolution instruments on demand by requesting an Agilent Dissolution Demo at Your Desk.
Learn more about MQ from the comprehensive Dissolution 1-on-1 Training Course on Agilent’s interactive resource site – the Agilent Dissolution Exchange. The Exchange provides a wealth of information on dissolution, support for solving laboratory challenges, and an opportunity to discuss dissolution topics with other analysts. For more tips and information on Agilent’s Dissolution Products, including the 280-DS Mechanical Qualification System, please contact your Agilent Sales Representative.
>> Update My Profile | Subscribe to Access Agilent | Article Directory