Access Agilent eNewsletter, July 2014
>> Update My Profile | Subscribe to Access Agilent | Article Directory
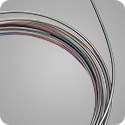
Surface deactivation improves GC analysis of reactive compounds
By John Oostdijk
Agilent GC R&D Chemist
Modern gas chromatography (GC) and gas chromatography/mass spectrometry (GC/MS) instruments are important analytical tools for accurate and reproducible measurement of many compounds at low ppb level in many matrixes. For accurate measurement, however, compounds need to survive the journey through the flow path. The flow path can contain different metal parts that need to be deactivated when analytes are more (re)active than alkanes. These include pesticides, alcohols, and other very polar compounds. Without surface deactivation, analytes can suffer from reversible interactions, giving peak tailing, and irreversible interactions (adsorption/reaction to the surface or catalytic break-down), resulting in lower recoveries. See the Agilent Inert Flow Path solutions primer for further information.
Significant improvement in stainless steel inertness
Agilent’s new UltiMetal Plus technology delivers a significant improvement in stainless steel inertness. UltiMetal Plus deactivation chemistries is applied specifically to steel and stainless steel surfaces and can be used safely when stainless steel products are prescribed in a method – for example, for unions, ferrules, tubing, backflush devices, the GC inlet weldment, and with selected detector parts. In this article we focus on Agilent UltiMetal Plus stainless steel capillary tubing as an alternative for commonly used fused silica. A comprehensive overview of UltiMetal Plus deactivation is available in Agilent publication 5991-3357EN.
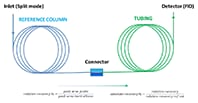
Figure 1. Principle of a tandem- or post-column test.
Testing tubing in tandem
As an example of this technology, we used a tandem column setup to verify tubing inertness (Figure 1). The compounds were first separated on a reference GC column, which was followed by a connector and a piece of tubing. The tubing was connected to a flame ionization detector. As system inertness was influenced by the total flow path, a system test was performed to establish the base level inertness profile. To be able to measure small differences in system activity, a high degree of initial inertness was required. The amount of analyte introduced in the column setup was calculated from the injection volume, split ratio, and concentration of the test mixture. Peak asymmetry and relative or absolute recoveries of several test components were the key parameters used to compare the inertness of connector and tubing parts.
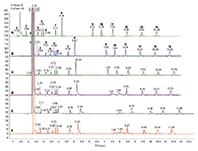
Figure 2. Comparison of different types of tubing, 5 m x 0.53 mm, using a very inert mix.
Agilent UltiMetal Plus improves performance
With Figure 2 we show a comparison of a tandem test of Agilent UltiMetal Plus 0.53 mm tubing. The inertness of the original UltiMetal product (developed 20 years ago), the newly developed UltiMetal Plus tubing, and tubing from a non-Agilent supplier were compared, using a very inert test mix.
All the stringent probes eluted and inertness was acceptable (although trimethylphosphate and 1,2-pentanediol show more tailing). Compared to the original UltiMetal tubing, the inertness improved significantly with the Agilent UltiMetal Plus technology. The non-Agilent product gave slightly more tailing. Further details are available in Agilent publication 5991-4499EN.
Agilent UltiMetal Plus: a cut above
UltiMetal Plus deactivation has no effect on the handling or cutting of tubing. To make a cut, you must hold the tubing carefully to avoid kinks, and then use the smooth side of a ceramic tubing cutter to score the tubing in the same place several times. Wipe the score with ethanol tissue to remove any loose particles. Finally, use the column cutter to keep the tubing straight as you bend it backwards and forwards. Inspect the cut end with a magnifying glass to ensure there are no burrs or jagged edges and that the bore diameter is unchanged. Recut if necessary. Full instructions can be found in Agilent publication 5991-3945EN.
Deactivation for successful trace analysis
Agilent applies Ultra Inert deactivation chemistry to all the critical parts in the GC system, including Ultra Inert liners. UltiMetal Plus technology is applied specifically to steel and stainless steel system parts such as unions, ferrules, tubing, backflush devices, the GC inlet weldment, and selected detector parts. See more of what Agilent deactivation can do for your trace analysis today.
>> Update My Profile | Subscribe to Access Agilent | Article Directory
Figure 2.
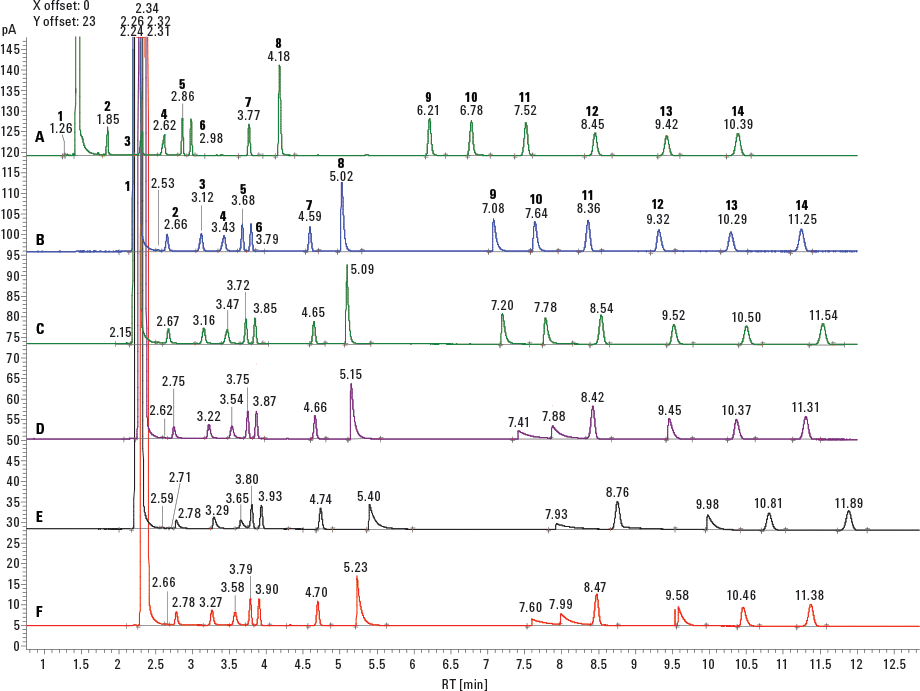
Peak no. |
Compound |
ng* |
---|---|---|
1 |
Methane |
|
2 |
Propionic acid |
1 |
3 |
iso-Butyric acid |
1 |
4 |
n-Butyric acid |
1 |
5 |
Octene |
0.5 |
6 |
Octane |
0.5 |
7 |
1-Nitrobutane |
1 |
8 |
4-Picoline |
2 |
9 |
Trimethyl phosphate |
5 |
10 |
1,2-Pentanediol |
2 |
11 |
Propylbenzene |
1 |
12 |
1-Heptanol |
1 |
13 |
3-Octanone |
1 |
14 |
Decane (used as 100% reference) |
1 |
*The calculated on-column amount after a split injection depended on the split ratio used.
Comparison of different types of tubing, 5 m x 0.53 mm, using the Very Inert Mix. A) system check with Agilent J&W VF-5ms (p/n CP8944) and Agilent Ultimate union (p/n G3182-60580); B) non-polar (apolar) deactivated fused silica; C) UltiMetal Plus guard, stainless steel (p/n CP6577); D) UltiMetal Plus tubing, stainless steel (p/n CP6581); E) UltiMetal tubing, stainless steel (p/n CP6540); F) non-Agilent inert deactivated tubing. Tubing was tested using the tandem setup at 60 °C with a constant hydrogen flow of 1.35 mL/min. On-column amounts and components are shown in above Table (split 1:75, 1 µL injection).